The sleeved plug valve is a non-lubricated type of plug valve that uses a sleeve component installed around the valve plug to maintain a continuous seal. The sleeve is used to provide the lubricity needed for the plug to rotate smoothly resulting in fast opening and closing of fluid flow. Sleeved plug valve manufacturers also use this sleeve to help reduce frequent maintenance needed in the lubricated type of valves as well as give the valve long service life. Sleeved plug valves are quarter valves. This is because they operate by turning the valve plug for a 90o degree angle to open or close. This type of sleeved plug valve operates manually or by use of actuators. Sleeved plug valves are designed such that the plug moves up slightly when opening fluid flow to ensure it leaves some clearance with the valve seat to avoid wear which can reduce service life of the plug. This type of plug valve has a tight shut-off and is used in various industrial applications such as waste water treatment, food processing, chemical processing, oil and gas among others.
Sleeved plug valve component:
In a sleeve plug valve, each component has its specific purpose for creating this robust valve design. The main components of a sleeve plug valve are the body, sleeve, cover, top seal, and cover are considered as main valve components.
Body: The body of a sleeved plug valve is cast as a one-piece that provides high integrity. This casting has integral design features that are important for creating key benefits of the product being cavity-free and maintenance-free.
The body casting has 360-degree lips around the ports which keep the sleeve in place preventing sleeve rotation while the valve is being operated. The sleeve relief area present in the body allows the PTFE sleeve to expand and contract during the temperature changes, this relief area also assists in controlling the valve torque.The body of the sleeve plug valve also consists of horizontal and vertical ribs which enables strong sealing capabilities between the sleeve and the plug by creating compression that is needed to maintain the sleeve in its place along with 360-degree lips.
Sleeve: A fluorocarbon sleeve that keeps the tapered plug in place and maintains a continuous seal. The sleeve provides the lubricity required to turn the valve, allowing it to open and close quickly, function without maintenance, be non-sticky, and last longer.
Top Seal: In sleeve plug valve design, the top seal ensures that fugitive emissions are kept to a minimum. It complies with or surpasses the most strict regulatory criteria currently in effect. The integrated, flexible graphite stem seal and the graphite cover seal ring ensure sealing where the stem and at the body/cover connects.
Cavity-free design: The cavity-free design is a significant feature of the sleeved plug valve and is crucial in applications where solids are present in the media. The key valve components the body the sleeve and the plug are in close contact with each other creating the cavity-free design. This means that there are no spaces between the plug and the body that can trap media when the valve is being operated.
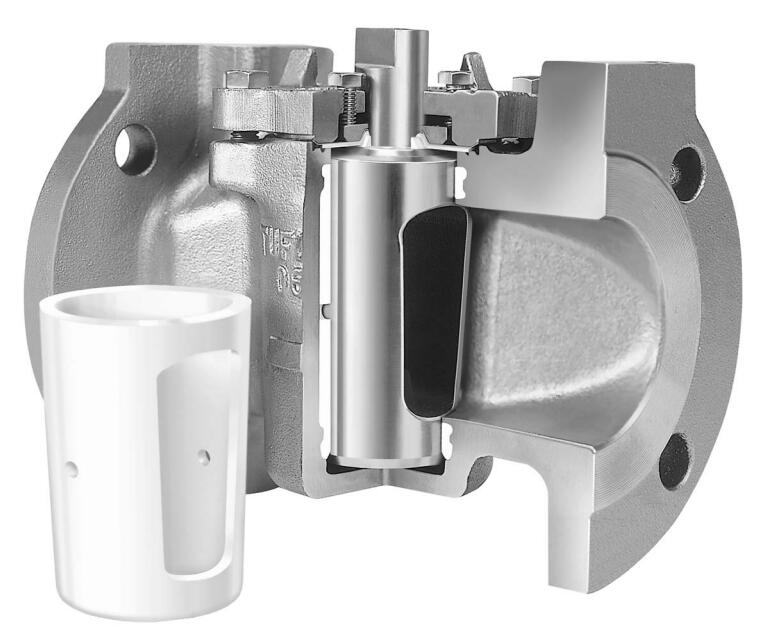
Sleeved plug valve structure feature
1. Design more economical, flexible, and compact fluid handling systems.
Bi-directional flow, simple actuation, lightweight, compact design, and multiport configurations all facilitate improved system design.
2. Superior, longer-lasting in-line sealing.
The inert PTFE sleeve completely surrounds the plug. The sleeve provides a large, circumferential sealing surface from port to port. Open, closed, or rotating, the seal is assured. No ball or gate valve can match this sealing power.
3. Secure sealing with no cold-flow, deformation, or rotation of the sleeve.
The sleeve is securely nestled in the sleeved plug valve body. High pressure ribs, top and bottom retention, and 360° port lips all assure sleeve containment.
4. No seizing. No sticking.
As the plug rotates, the 360° port lips provide a self-cleaning action to remove scaling and adhering media.
5. No cavities. No contamination.
There are no body cavities where flow media can accumulate and contaminate future processing. This cavity-free design also prevents sticking.
Types of sleeved plug valve
2 Way sleeved plug valve
This is a sleeved plug valve designed with two way valve ports. Sleeved plug valve manufacturers design this type of plug valve for use in medium-pressure applications. 2 Way sleeved plug valve is non-lubricated structure, soft seated for zero leakage.
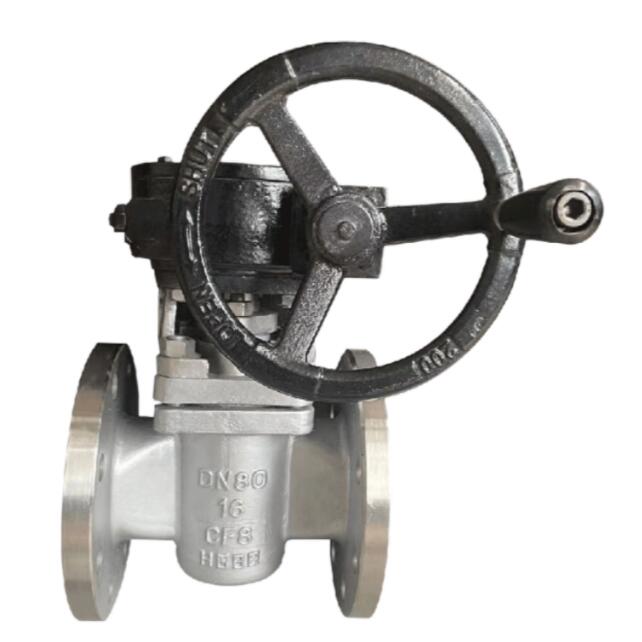
3 Way sleeved plug valve
This is a sleeved plug valve designed with three valve ports. Sleeved plug valve manufacturers design this valve to help reduce the cost of buying three gate valves for the same task. With this type of sleeved plug valve, one can transport fluid in different lines as well as use the same valve to divert or mix the fluid. When used to mix fluid, 3 way sleeved plug valve gets fluid from two pipes and mixes the two fluids to leave the valve as one fluid stream. For diversion of fluid, one fluid stream enters the sleeved plug valve and the plug valve port changes its direction of flow to an angle of 90o degrees. This type of 3 way sleeved plug valve makes the cost of the piping system cheaper relative to using several gate valves.
Threaded end sleeved plug valve
This is a sleeved plug valve that is connected to the pipe using threads. Sleeved plug valve manufacturers design this type of valve for use in medium-pressure applications. The sleeved plug valve ports are designed with threaded ends. The pipe end to be connected to the sleeved plug valve is also has threads machined on the end. The threads are male and female such that if the valve has female threads the pipe end should have male threads and vice versa. This type of sleeved plug valve is easy to assemble and small in size relative to the bolted type.
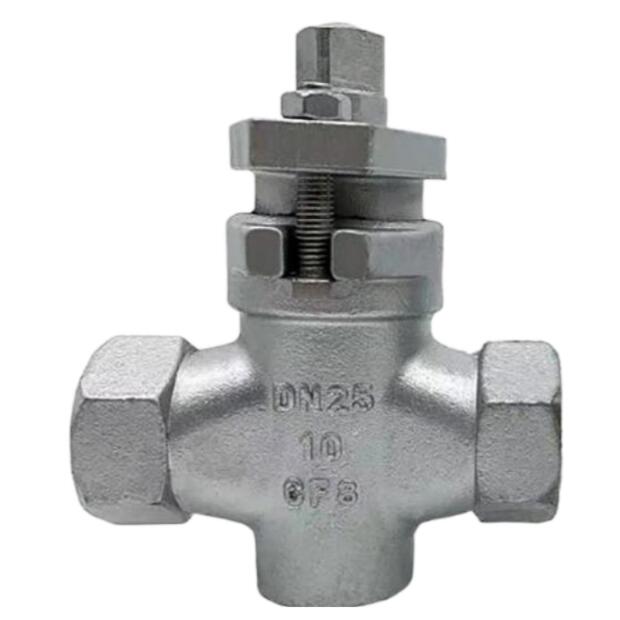
Flanged end sleeved plug valve
This is a sleeved plug valve that is connected to the pipe using bolts and nuts. Sleeved plug valve manufacturers design this valve with flanged ends on the exit and outlet ports. These flanged ends also have holes drilled on them. The pipe to be connected to the sleeved plug valve also has flanged ends and holes drilled on it. The flanged ends on the valve and pipe are equal. This type of valve is suitable for use in high-pressure applications as it ensures no fluid leakage due to high torque strength enhanced by several bolts and nuts used. The problem associated with this type of plug valve is that it is usually heavy relative to the welded end and threaded end valve types due to the several bolts and nuts used to tighten it. Also, this sleeved plug valve is large relative to other valves and thus it occupies large area when installed.
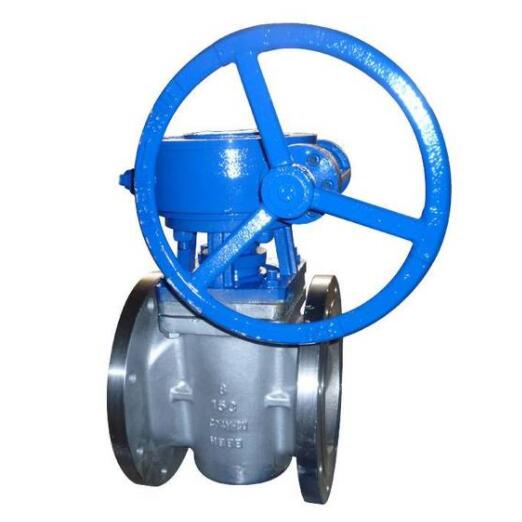
Welded end sleeved plug valve
This is a sleeved plug valve that is connected to the pipe by through welding method. This valve is very reliable as it ensures that no fluid can leak through the valve body-pipe connection due to loose bolts or screw threads. The valve port end and the pipe ends are welded together creating a solid connection free from any flaws that may lead to leakage. Such a sleeved plug valve is suitable for use in applications that involve very hazardous and corrosive media which, in case of any slight leakage may lead to damage to the environment or injury to the valve personnel. The weld has to be removed first before removing this sleeved plug valve from the piping system for repairs.
How does a sleeved plug valve work?
This sleeved plug valve operates by using a handwheel/hand lever or by use of an actuator. Whether the sleeved plug valve is manual or automatic, the working mechanism is the same. The plug valve starts when the handwheel/ actuator rotates forcing the stem as well as the plug valve plug to rotate. To open the sleeved plug valve, the handwheel/actuator rotates the plug valve stem for a quarter turn in the clockwise direction. The rotation of the stem in the clockwise direction forces the valve plug to rotate for a 90o degree where it aligns the plug port collinear to the valve port. This creates an unobstructed path for the fluid to flow through the sleeved plug valve. To close the fluid flow, the handwheel/actuator rotates in the counterclockwise direction for a quarter turn. This then forces the stem and thus the plug to make the same 90o degree turn which positions the plug port normal to the valve port. This ensures the valve plug is blocking the fluid flow and thus no fluid can flow through the sleeved plug valve. For throttling fluid flow, the handwheel is rotated for an angle of around 45 degrees to allow some space for the fluid to flow through the valve. Sleeved plug valve manufacturers recommend use of this valve in throttling fluid flow where pressure drop will not cause technical challenges since throttling causes pressure drop by a great margin.
Sleeved plug valve performance feature:
1. These sleeved plug valves have an economical and compact design, bi-directional in nature, actuation is very simple, lightweight, and the fluid handling system is flexible and compact.
2. The plug is entirely enveloped in an inert PTFE sleeve. From port to port, the sleeve offers a broad circumferential sealing surface. The sealing is guaranteed whether the valve is open, closed, or turning. This sealing capability cannot be matched by any ball or gate valve.
3. The sleeve is firmly inserted into the body of the valve. Sleeve confinement is ensured by high-pressure ribs, top and bottom retention, and 360° port lips present in this design.
4. The 360° port lips enable a self-cleaning action as the plug rotates, removing scaling and sticking material due to which there is no seizure and sticking of the plug.
5. The friction coefficient of the PTFE sleeve is very low. It has lubricating properties. Even if the valve is kept unoperated in any condition for long periods of time, ease of operation is ensured.
6. Standard pricing and a significantly prolonged service life ensure extremely lower long-term costs of ownership.
7. The stem sealing on the sleeve plug valve is made up of cup springs that guarantee consistent forces acting on the sealing element and the plug. This results in zero emissions and a longer life cycle.
8. There are no cavities in the body where flow material can collect and contaminate subsequent processing. This cavity-free construction also keeps things from sticking together.
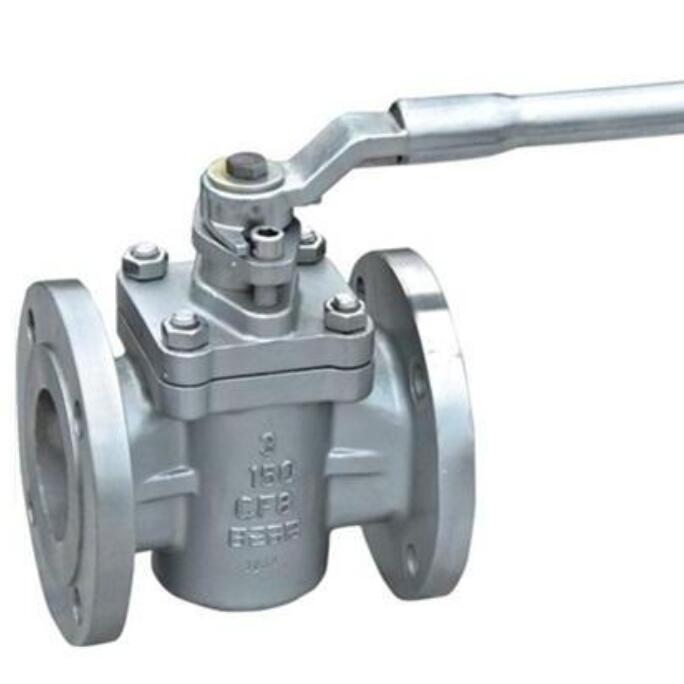
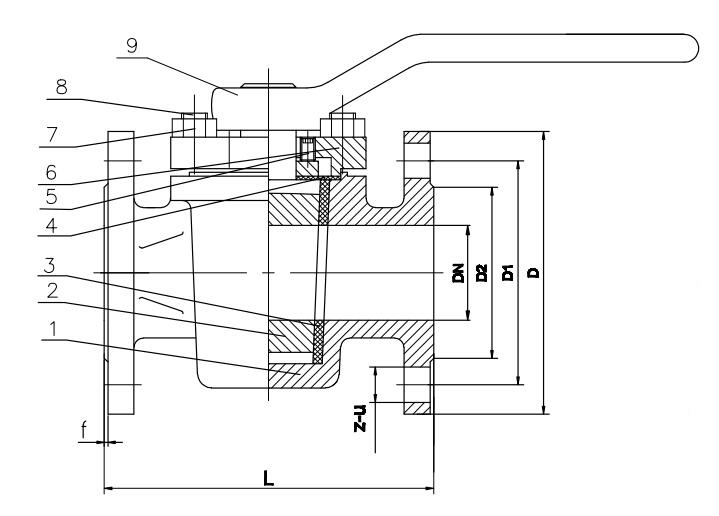